In line with forthcoming legislation, we are conducting an environmental risk assessment of our Global Supply Chain business partners. This assessment will be conducted by independent specialist consultants.
The insights we gain from the assessment will be used to upgrade our factory assessment methodology, policies, and environmental risk mitigation work going forward.
Our supply chain is where we have the biggest environmental impact, therefore, strong cooperation with our suppliers and incentivising them to reduce the consumption of water, chemicals, energy and the production of waste, is vital to our success.
Each factory must meet our Environmental Management Requirements, which you can read in the document attached below. This document outlines standards and expectations on chemical and environmental management at all factories that supply BESTSELLER orders. Each factory's performance is used as the basis for the wider environmental rating applied to each supplier.
Factory assesment
The factories are assessed on the following. Please note this is not an exhaustive list, which you can read in this document.
The factories that produce BESTSELLER products must comply with all applicable environment and chemical laws in their jurisdiction. This includes adherence to the permits, authorisations, licenses, registrations, certificates, waste/effluent treatment contracts, and other compliance requirements.
BESTSELLER uses the Higg Facility Environment Module (FEM) tool as one part of its environmental performance evaluation for factories in our supply chain. All key factories of BESTSELLER need to adopt the Higg FEM so we can measure environmental performance across seven impact areas: environmental management systems, water use, wastewater, chemical use, waste management, energy use and greenhouse gas emissions. The use of Higg FEM means this data is consistently recorded and tracked across all sourcing markets.
BESTSELLER requires all factories involved in the creation of our products to have a clearly defined and effectively implemented EMS. An effective EMS is essential in order to understand and address potential risks and impacts, to achieve legal compliance, and to work towards continuous environmental improvement.
BESTSELLER requires factories to reduce greenhouse gas emissions by reducing the total amount of energy used at their facility and/or by switching to cleaner fuel sources. To achieve the goal, all factories should identify and track all sources of energy that are used and set a normalised baseline for energy use. They are also required to set targets with accompanying action plans and demonstrate progress.
Beyond comply with local laws and ZDHC Wastewater Guidelines, all wastewater from both industrial processes and domestic processes must be treated onsite before being pumped out of the facility –or it must be sent to an approved and licensed treatment centre. Uncontrolled discharge of untreated wastewater is a zero-tolerance issue for BETSELLER and will result in a halt on orders.
To ensure our products are meeting the standard set in the RSL, we have a Chemical Testing Programme, which must be followed by all manufacturers. Testing is performed based on risk, suppliers that are unable to meet the Chemical Restrictions are placed under ‘observation’, and a high level of product chemical testing is required. You can read more about our Chemical Testing regime below.
Factories with wet process should identify and track the quantity of water the facility withdraws from all sources and set normalised baseline for water use and identify which factors (processes, machines or operations) contribute most to water use on site.
Factories are required to track all hazardous and non-hazardous waste streams, record and report the volume generated and disposal method for all hazardous and non-hazardous waste streams. All waste must be properly segregated and stored, and workers must be trained in the handling of all hazardous and non-hazardous waste streams.
Factories must know sources of air emissions from operations and onsite processes.
Promoting environmental stewardship
Supplier Environment Rating
To meet our targets on climate, water, and circularity our products need to be consolidated in suppliers that are willing to move forwards with us on this journey.
By 2025, we have committed in our Fashion FWD strategy that 75% of all product orders will be placed with suppliers that are highly rated in our Sustainability Evaluation. A supplier’s environmental performance is a very important part of this criteria. We use data from the Factory Standards Programme, Higg FEM (see below), BHive, and the IPE to create the Supplier Environment Rating.
Brands are monitored on the rating of suppliers they buy products from. Our local Chemical & Environmental teams also provide guidance and support during routine inspections and afterwards.
One tool we use is the Higg Facility Environmental Module (Higg FEM) Index, which is designed for the apparel and footwear industry to measure performance across seven impact areas, environmental management systems, water use, wastewater, chemical use, waste management, energy use and greenhouse gas emissions. Higg FEM is an industry-wide tool developed by the Sustainable Apparel Coalition (SAC).
In China, BESTSELLER cooperates with the Institute of Public Affairs (IPE), a non-profit environmental research organisation based in Beijing that monitors many aspects of environmental supply chain management and records suppliers’ performance on a public database.
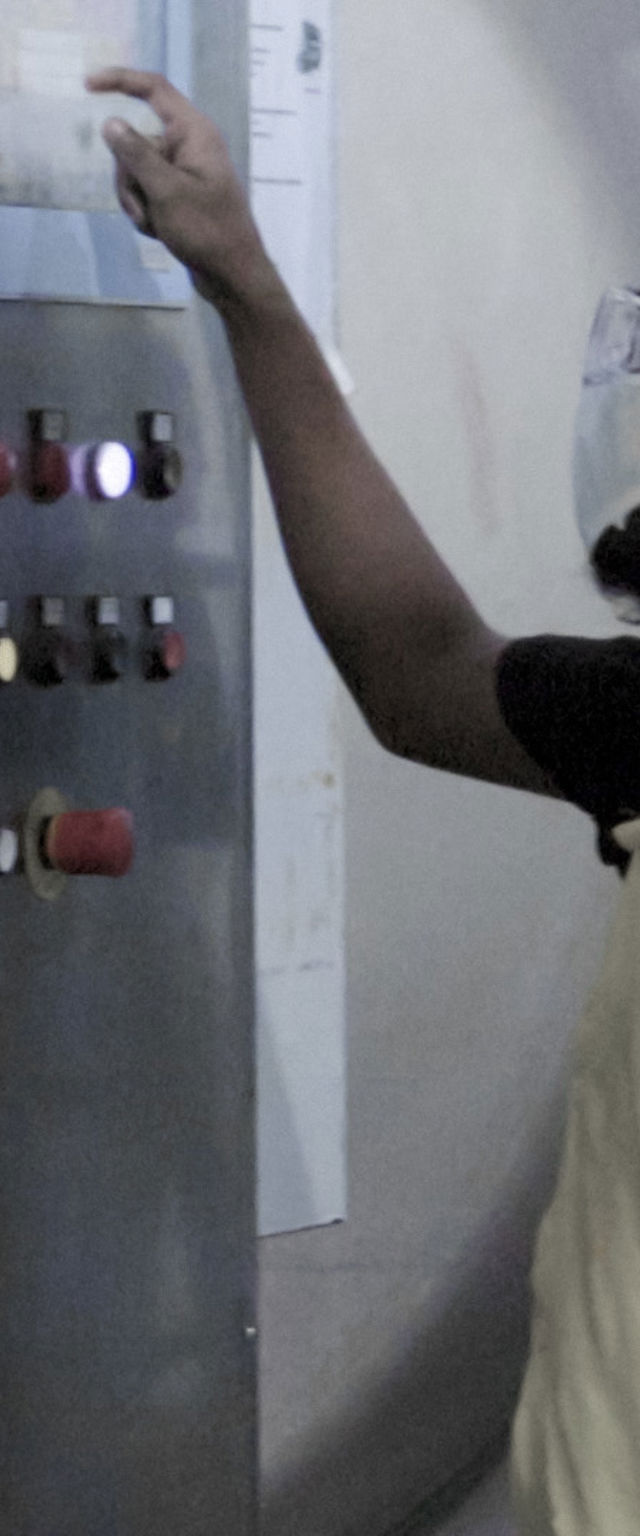
Monitoring product safety: Chemicals
Chemicals are used in each stage of the production of garments and footwear. In BESTSELLER we manage chemical risk on two levels.
Firstly, we work closely with our suppliers to ensure that they are managing their chemical inventory. Through our Factory Standards Programme, which covers all Tier 1 production and Tier 2 tanneries, we systematically check whether the factories have protocols in place for the safe handling of chemicals. We require all factories to maintain and provide us with a chemical inventory list (CIL) of the chemicals kept on site. During factory assessments, our assessors check that safety precautions in regards to the use, storage and handling of chemicals are being taken, and that employees are provided with protective equipment and have been sufficiently trained in handling chemicals.
On the second level, we have a thorough Chemicals Testing Programme to ensure all products meet our requirements. Our Restricted Substances List (RSL) and Packaging Restricted Substances List (PRSL) catalogue chemicals that are banned or restricted in our final products. It is updated annually based on the latest legislation, AFIRM guidelines, as well as precautionary principles and industry best practice, and shared with suppliers.
Through our Chemical Testing Programme, we systematically test our products and materials at accredited global independent laboratories approved by BESTSELLER to ensure that all products made for us comply with our requirements, and rework those that do not meet these requirements.

Promoting responsible chemical-usage
Responsible management of chemicals is an industry-wide challenge. To develop an industry-wide culture of responsible chemical usage and management, we engage with multiple platforms and fund intiatives, such as the development of and piloting of GoBlu's BHive app.
BESTSELLER is a member of Swedish non-profit ChemSec's PFAS Movement, which advocates for reducing the use of PFAS in the apparel manufacturing industry. Their 'No to PFAS' campaign brings together companies and organisations to accelerate legislation on hazardous substances.
ChemSec wants to create a strong link between researchers, decision makers and companies in the fight against harmful chemicals. Through ChemSec's PFAS movement, companies commit themselves to getting hazardous fluorides covered by EU chemicals legislation, REACH, which lists the harmful chemicals that are banned from use in the EU.
BESTSELLER is a member of the AFIRM group whose mission is to reduce the use and impact of harmful substances in the apparel and footwear supply chain. Through our engagement in AFIRM, we can align with the industry on restricted substances, the limits to be set, test methods and chemical investigations and responses to legislative updates.
AFIRM provides a unique forum to discuss chemical details, legislative changes and different materials. It is also a great resource for us and other companies like us, as it produces materials in various languages that we can use in training for suppliers and stakeholders. We recently developed a sampling guide, a resource instructing brands on how to run chemical test on product samples. We have shared this guide with AFRIM members, to share and align best practices with our industry partners who may not have the resources to develop this internally.
BESTSELLER also participates in multi-brand collaborative studies. One example of this was on the chemical content of post-consumer recycled textiles. The study, which was led by H&M and IKEA Group, was investigating the presence of legacy chemicals and potentially hazardous chemicals in recycled materials, a key roadblock to realising circularity in the textile industry. For the study, post-consumer cotton, wool, and polyester waste sourced from different regions of the world were tested, resulting in a total of 70,080 data points. After pooling and analysing the data, the group found that 2.5% of the data points showed undesirable detections, but less than 1% of the data points exceeded AFIRM RSL2 limits. The study found that there are significant risks posed by incorporating post-consumer cotton, wool and polyester into new products.
The results of the study will be used to advocate for establishing an acknowledged and harmonised hazard assessment methodology for chemicals used in production, restricting the use of chemicals that hamper the recyclability of products.